Is it true that metal over cladding can greatly enhance a building’s performance and aesthetics? You might find that its durability and weather resistance offer more than just protection; they can also lead to long-term cost savings and lower maintenance needs. But that’s just scratching the surface. When you consider energy efficiency and the potential for a visually appealing design, the discussion opens up even further. What other advantages might you uncover that could influence your next construction decision?
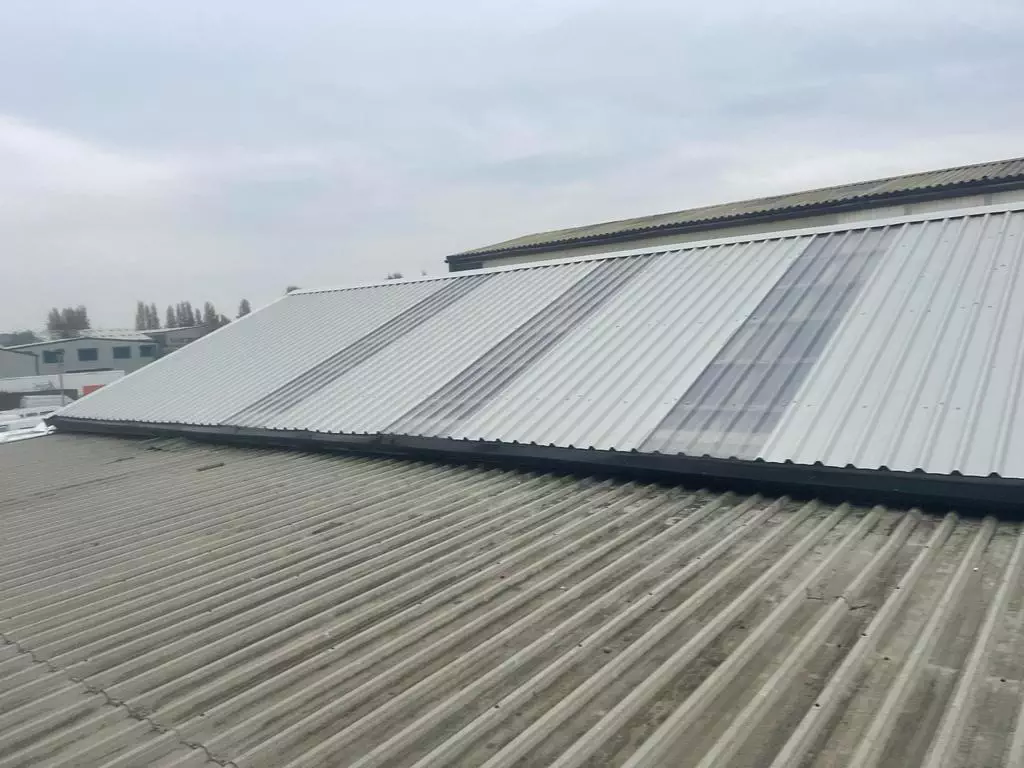
Understanding Asbestos Over cladding
Asbestos overcladding refers to the process of applying a new cladding system over existing structures that contain asbestos materials. This method serves as a practical solution for mitigating asbestos risks while enhancing building aesthetics and energy efficiency. By encapsulating the asbestos, you effectively reduce the chances of fiber release, which can lead to serious health issues.
When you consider overcladding, it’s vital to weigh the benefits it offers. First, it provides an effective barrier that protects occupants from potential exposure to harmful asbestos fibers. Second, this process can improve thermal insulation, thereby lowering energy costs over time. Additionally, overcladding can modernize the appearance of a building without the need for extensive demolition, minimizing disruption.
However, it’s important to verify that the overcladding installation is performed by professionals trained in handling asbestos-containing materials. This expertise guarantees that the project adheres to safety regulations, reducing the likelihood of asbestos risks during and after installation.
Understanding the balance between the potential hazards of existing asbestos and the benefits of overcladding will help you make informed decisions regarding your building’s future.
Factors Influencing Costs
Several factors can substantially influence the costs associated with asbestos overcladding projects. One major consideration is the health risks tied to asbestos exposure. If your building has significant asbestos issues, you’ll need specialized contractors for safe removal or encapsulation, which can drive up labor costs.
Additionally, the complexity of the project plays a critical role in determining expenses. If your building has intricate architectural features or requires extensive structural modifications, it could extend project timelines and increase costs.
Permitting and regulatory requirements also come into play. Depending on your location, the need for environmental assessments or compliance with strict safety regulations can add both time and expense to the project.
Lastly, the availability of skilled labor and materials can impact costs. If demand for asbestos remediation services is high, you might face inflated prices. Conversely, delays in material procurement can lead to extended project timelines, further escalating costs.
Material Options and Pricing
When considering material options for asbestos overcladding, it’s vital to evaluate both the types of materials available and their associated costs.
You’ll typically find options like fiber cement, metal panels, and vinyl siding, each offering distinct advantages. Fiber cement, known for its exceptional material durability, usually ranges from $2 to $6 per square foot. Metal panels, while slightly higher at $5 to $10 per square foot, provide a sleek, modern look that many find appealing. Vinyl siding, more budget-friendly at $1 to $4 per square foot, boasts low maintenance but may not match the durability of the other options.
Aesthetic considerations also play an important role in your decision-making. For instance, if you’re aiming for a contemporary facade, metal panels might be the best fit, while traditional styles might benefit from the charm of fiber cement.
Keep in mind that while upfront costs are important, long-term durability and maintenance should influence your choice as well. Ultimately, balancing your budget with your aesthetic vision will lead you to the most suitable material for your asbestos overcladding project.
Labor and Installation Expenses
Considering labor and installation expenses is vital for any asbestos overcladding project. These costs can greatly impact your overall budget. You’ll want to evaluate labor efficiency and installation techniques to guarantee ideal resource allocation.
Labor efficiency varies based on the crew’s experience and the complexity of the job. Skilled workers won’t only complete the installation faster but also minimize the risk of errors that could lead to costly rework. Be sure to assess the qualifications of your chosen team and their familiarity with asbestos-related procedures.
Installation techniques also play an important role in determining labor costs. Advanced methods, such as panelized systems or modular components, can streamline the process, reducing both time and labor. On the other hand, traditional installation methods may require more extensive labor hours, increasing overall expenses.
It’s essential to get detailed quotes that break down labor and installation costs, including any additional charges for specialized equipment or safety measures.
Regulatory Compliance Costs
Regulatory compliance costs represent a fundamental aspect of any asbestos overcladding project. You’ll need to navigate a complex web of regulatory guidelines that govern the use of asbestos and its management. These guidelines can vary greatly depending on your location, making it imperative to stay informed about local regulations and requirements.
When you initiate an overcladding project, you should factor in costs associated with compliance audits. These audits are essential for verifying adherence to the established standards and can uncover potential issues before they escalate. If you fail to comply, you might face hefty fines or project delays, which can inflate overall expenses.
Additionally, hiring specialists to guarantee compliance can add to your costs. These experts won’t only help you interpret regulatory guidelines but also assist in developing a thorough plan for safe asbestos management.
Training your staff to recognize and respond to compliance requirements is another important investment.
Ultimately, understanding and budgeting for regulatory compliance costs is critical for the success of your asbestos overcladding project. Ignoring these factors can lead to considerable financial repercussions and jeopardize your project’s timeline.
Frequently Asked Questions
How Can I Identify Asbestos in My Building?
To identify asbestos in your building, inspect older building materials, especially insulation, flooring, and ceiling tiles. Conduct asbestos testing with a certified professional to guarantee safety and accurate identification of any hazardous materials present.
What Are the Health Risks Associated With Asbestos Exposure?
Asbestos exposure poses serious health risks, including lung cancer and asbestosis. You should be aware of exposure sources and comply with asbestos regulations to minimize your risk and guarantee a safer environment for yourself and others.
Is Asbestos Overcladding Necessary for All Buildings?
Think of asbestos overcladding as a protective shield. It isn’t necessary for every building; however, you should conduct thorough building assessments and follow asbestos regulations to determine if it’s essential for your specific structure.
Can I Perform Asbestos Overcladding Myself?
You can’t perform asbestos overcladding yourself without adhering to strict DIY regulations. Handling overcladding materials requires specialized knowledge and safety measures due to the potential health risks associated with asbestos exposure. Always consult professionals for such tasks.
What Are the Long-Term Benefits of Asbestos Overcladding?
When you consider asbestos overcladding, you’ll enhance building aesthetics while complying with asbestos regulations. This can increase property value, improve energy efficiency, and reduce maintenance needs, ultimately providing long-term benefits for both you and your investment.
Conclusion
In summary, traversing asbestos overcladding costs requires a careful assessment of materials, labor, and compliance. For instance, a homeowner opting for fiber cement may spend around $15,000, while choosing metal panels could push costs to $25,000. Balancing budget constraints with the long-term benefits of energy efficiency and durability is essential. By weighing these factors, you can make an informed decision that not only meets aesthetic goals but also guarantees safety and compliance in your renovation project.